We offer an advanced robotic station designed to automate the crucial manufacturing stage in the marine industry – the lamination of yacht, boat, and sailboat hulls. Our solution guarantees repeatability, the highest quality, and a significant increase in process efficiency. Moreover, it ensures operational safety in an explosive atmosphere.
Robotic Station for Automated Hull Lamination

Key Features and Functionality of the Station
- Automated Laminate Roll-Out: The robot’s primary task is the precise rolling-out of saturated fiberglass (wet laminate) using a specialized head with a tensometer, ensuring perfect pressure and the removal of air bubbles.
- Hybrid Operation (Robot + Operator): The station is designed for flexibility. Therefore, its layout allows for parallel manual work by operators in a separate area while the robot performs its tasks, maximizing the use of time and space.
- Integrated Rotary Positioners (7th Axis): Two positioners act as an additional, synchronized axis for the robot. They enable the precise rotation of the hull, giving the robot access to hard-to-reach areas while maintaining optimal process parameters (tool attack angle, pressure, etc.).
- Top-Tier Components:
- Control system based on reliable Siemens S7-1500 controllers.
- Pneumatic system (air preparation unit, valves) based on proven solutions from SMC.
- Safety in Ex-Zone: The device is fully compliant with safety requirements for operation in an explosive atmosphere (Zone 2).
- Manual Station Setup: Preparing and mounting the lamination molds is done in a simple and proven manual manner.
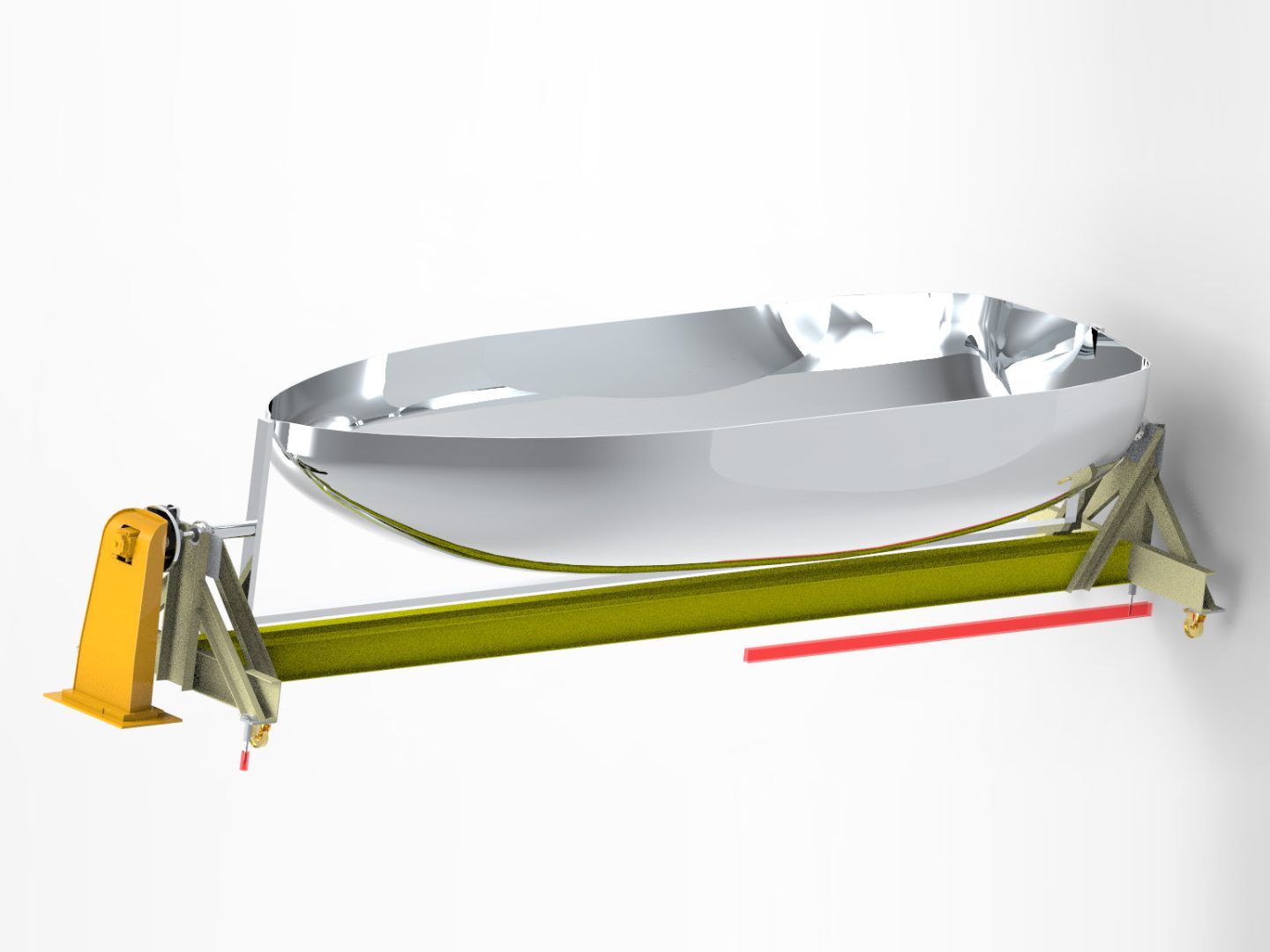
Main Equipment of the Station
- 6-axis industrial robot adapted for work in harsh conditions.
- Linear track with dustproof covers on which the robot moves.
- Steel support structure for the track and robot, ensuring stability.
- Two rotary positioners with a coupling mechanism for the hull transport carriage.
- Positioning system (holes and rails) for precisely locating the mold carriage at the station.
- Dedicated roll-out tools in the form of a head with a tensometer and an exchangeable roller.
- Central control cabinet integrating all systems.
- Full safety enclosure (dimensions approx. 4.5 × 23 × 2 m) with a sliding gate and three service doors.
- Overall dimensions of the entire device with the enclosure: approx. 4.5 × 23 × 4 m.
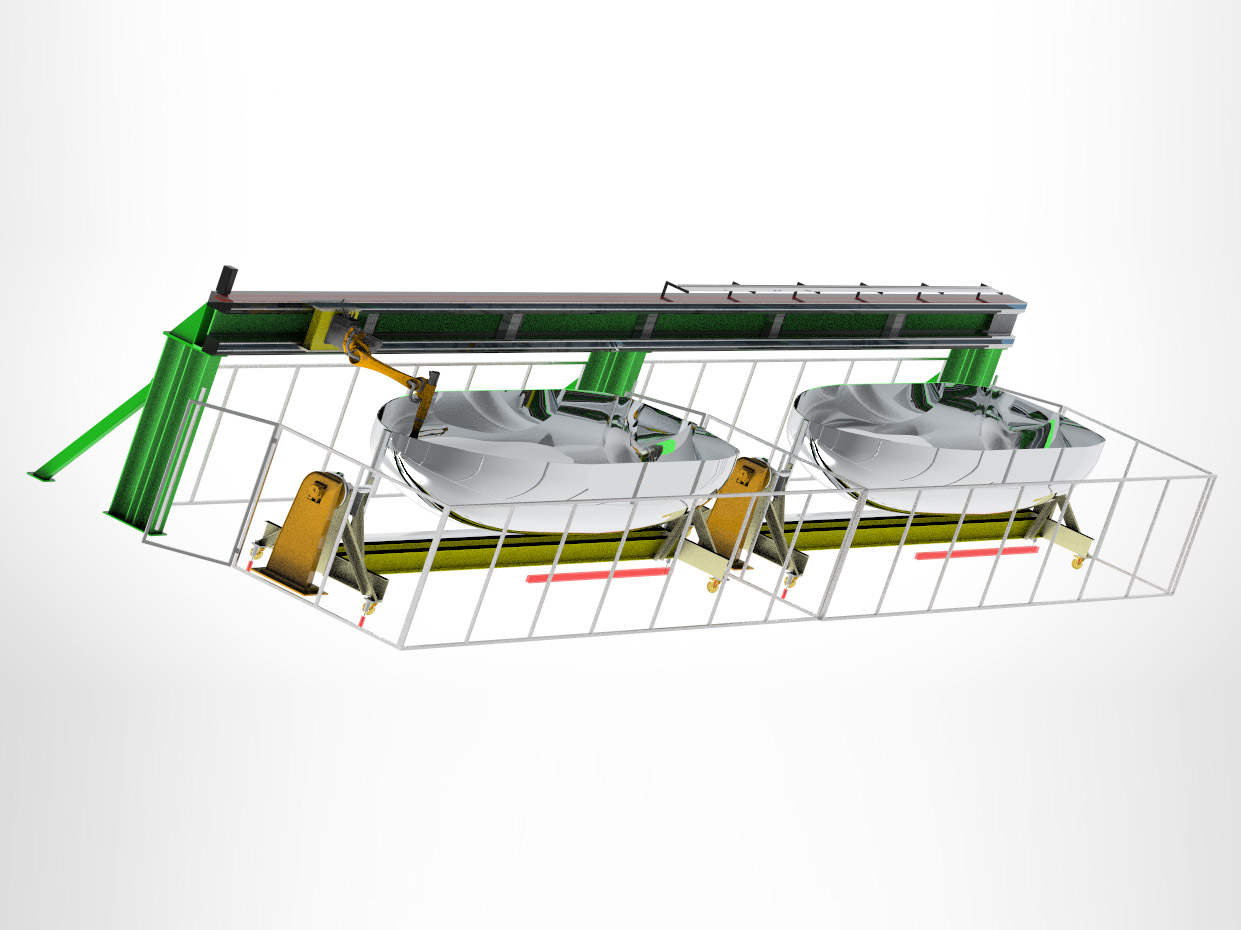
Optimized Hybrid Work Cycle
The proposed work cycle ensures maximum efficiency through the parallel operation of operators and the robot:
- Step 1: Workers perform the initial resin saturation of area 1 of the hull.
- Step 2: The robot begins rolling out the finished area 1, while workers simultaneously prepare (saturate) area 2.
- Step 3: The robot moves to roll out area 2, and the workers return to prepare the next section in area 1.
- As a result, the cycle repeats alternately, ensuring continuous work and eliminating downtime until the entire programmed surface of the hull is completed.
Optional Functional Extensions
In addition, the station can be expanded with additional capabilities (available as a separate quote):
- Automated resin and hardener spraying.
- Automated gelcoat spraying.
- Automated chopped fiber spraying with resin and hardener (roving).
Contact us to discuss your project details.
Back
to top